عوامل محیطی تاثیرگذار بر طول عمر فولاد
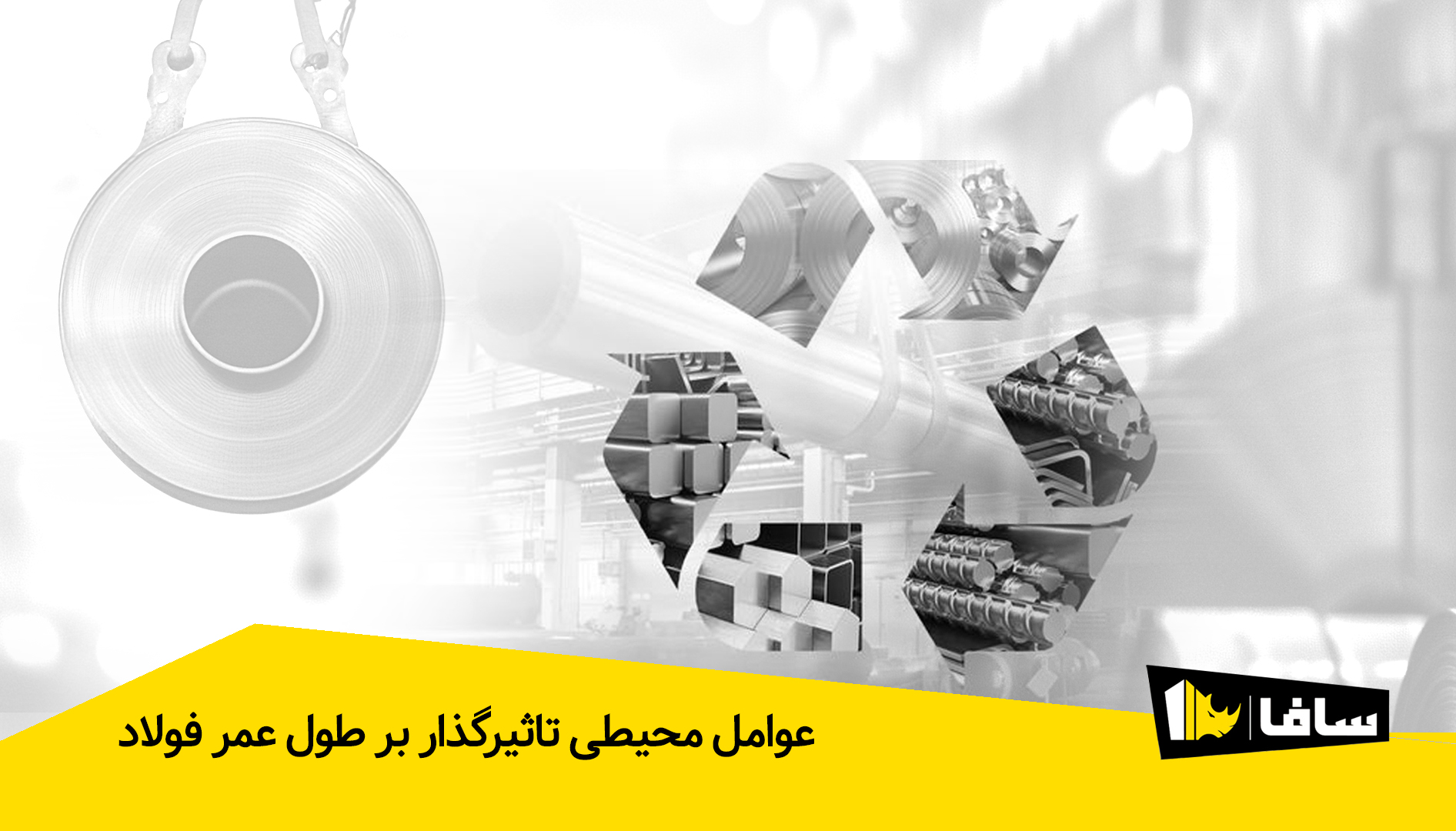
فولاد یکی از پر کاربرد ترین و پر استفاده ترین جز مورد استفاده در تمام پروژه های عمرانی و صنعتی می باشد که نقش حیاتی در زندگی روزمره ما ایفا میکند. از ساختمانهای بلند و سازه های عظیم شهری گرفته تا انواع پلها، خودروها و کشتی ها و هواپیما و فضاپیماها و تجهیزات صنعتی، همه جا اثری از این آلیاژ مستحکم و کاربردی دیده میشود. طبیعتا کیفیت و میزان استقامت و به عبارتی طول عمر مفید هر فولادی با فولاد دیگری می تواند متفاوت باشد. دلیل این امر هم کاملا مشخص است؛ آن هم این است که هر فولاد برای مقاصد خاصی طراحی و تولید می شود. اما با این حال، هر فولاد با هر درجه کیفی و با هر استانداردی هم که ساخته شده باشد تنها برای یک مدت زمان مشخصی قابل استفاده و بهره برداری می باشد و بلاخره پس از چندین دهه فرسوده می شود. یک سری عامل و شرایطی در محیط هایی که در آن از فولاد استفاده می شود وجود داشته که هر کدام از آن ها به تنهایی می توانند عمر مفید فولاد کاهش دهند و منجر به خسارات و آسیب های جبران ناپذیری شوند.
ما در جدید ترین محتوای سافا می خواهیم به بررسی دقیق عوامل محیطی موثر بر طول عمر فولاد بپردازیم. ما با شناخت این عوامل، میتوانیم درک بهتری از چگونگی محافظت و افزایش طول عمر سازهها پیدا کنیم و از سرمایههای خود به نحو احسن بهرهبرداری نماییم. پس مثل همیشه همراه ما باشید.
معرفی عوامل محیطی و تاثیرات آن ها
منظور از عوامل محیطی کلیه عوامل و پارامترهایی است که فولاد در محیطی که مورد استفاده واقع شده در معرض آن ها است. عواملی همچون دما و حرارت محیط، میزان رطوبت، آلاینده های موجود در محیط، میزان گرد و خاک و...از دسته عوامل محیطی به حساب می آیند. در ادامه مهم ترین عوامل محیطی تاثیر گذار بر روی طول عمر فولاد را توضیح می دهیم:
- خوردگی و زنگ زدگی
خوردگی یکی از مهمترین عوامل موثر بر کاهش طول عمر فولاد است. این پدیده زمانی رخ میدهد که فلز در تماس با محیطی قرار گیرد که امکان انجام واکنشهای شیمیایی یا الکتروشیمیایی را فراهم کند. در نتیجه این واکنشها، فلز به تدریج تخریب شده و خواص مکانیکی خود را از دست میدهد.
فرایند خوردگی به چه صورتی است؟
خوردگی فولاد معمولاً به صورت یک واکنش الکتروشیمیایی رخ میدهد. در این واکنش، آهن موجود در فولاد الکترون از دست داده و به یون آهن تبدیل میشود. الکترونهای آزاد شده به سمت کاتد حرکت کرده و در آنجا با اکسیژن و آب واکنش میدهند و هیدروکسید آهن (زنگ) را تشکیل میدهند.
انواع خوردگی فولاد عبارتند از:
خوردگی یکنواخت: رایجترین نوع خوردگی است که در آن تمام سطح فلز به طور یکنواخت تحت تأثیر قرار میگیرد. این نوع خوردگی به راحتی قابل تشخیص است زیرا ضخامت فلز به طور یکنواخت کاهش مییابد.
خوردگی گالوانیکی: زمانی رخ میدهد که دو فلز متفاوت در تماس با یکدیگر و در حضور یک الکترولیت (مانند آب شور) قرار بگیرند. فلز فعالتر به عنوان آند عمل کرده و خوردگی پیدا میکند، در حالی که فلز نجیب تر به عنوان کاتد عمل کرده و در برابر خوردگی مقاومتر عمل می کند.
خوردگی حفرهای: این نوع خوردگی در حقیقت، ایجاد حفرههای کوچک و عمیقی در سطح فلز است که به تدریج بزرگتر شده و به عمق فلز نفوذ میکند. این نوع خوردگی بسیار خطرناک است زیرا از بیرون قابل مشاهده نیست و ممکن است به طور ناگهانی منجر به شکست سازه شود.
خوردگی تنشی: زمانی رخ میدهد که فلز تحت تنش مکانیکی و در معرض یک محیط خورنده قرار گیرد. این ترکیب باعث ایجاد ترکهای ریز در فلز شده و سرعت خوردگی را افزایش میدهد.
خوردگی بین دانهای: خوردگی در مرز دانههای فلز رخ میدهد و معمولاً در فولادهای ضد زنگ مشاهده میشود. این نوع خوردگی به دلیل تفاوت در ترکیب شیمیایی مرز دانهها نسبت به داخل دانهها رخ میدهد.
عواقب آسیب دیدن فولاد بر اثر خوردگی چیست؟
کاهش مقاومت مکانیکی: کاهش ضخامت فلز و ایجاد حفرهها، باعث کاهش مقاومت مکانیکی سازه میشود.
کاهش طول عمر: خوردگی به تدریج باعث تخریب فلز شده و عمر مفید سازه را کاهش میدهد.
افزایش هزینههای تعمیر و نگهداری: برای جلوگیری از خرابی کامل سازه، نیاز به انجام تعمیرات و نگهداری مداوم است که هزینههای زیادی را به دنبال دارد.
خطرات ایمنی: خوردگی میتواند باعث ایجاد ترک و شکست ناگهانی سازه شده و خطرات جانی و مالی را به دنبال داشته باشد.
- میزان دما و حرارت محیط
دما یکی از عوامل بسیار مهم و تاثیرگذار بر طول عمر فولاد است. تغییرات دما میتوانند به طور مستقیم بر خواص مکانیکی فولاد و در نتیجه بر مقاومت آن در برابر خوردگی و سایر عوامل تخریبکننده تأثیر بگذارند.
تاثیر دما بر فولاد به چه صورتی است؟
تغییر ساختار کریستالی: با تغییر دما، ساختار کریستالی فولاد میتواند تغییر کند. این تغییر ساختار باعث تغییر در خواص مکانیکی فولاد میشود.
تغییر در مکانیسمهای تغییر شکل: در دماهای بالا، مکانیسمهای تغییر شکل مانند لغزش و دوقلو شدن اتمها آسانتر انجام میشود.
تغییر در سرعت انتشار اتمها: با افزایش دما، سرعت انتشار اتمها در شبکه کریستالی افزایش یافته و این امر باعث تسریع فرآیندهای مانند خوردگی و خزش میشود.
تاثیر دماهای بالا بر فولاد
کاهش مقاومت مکانیکی: با افزایش دما، اتمهای فولاد انرژی جنبشی بیشتری پیدا کرده و از یکدیگر دور میشوند. این امر باعث کاهش پیوندهای بین اتمها و در نتیجه کاهش استحکام و سختی فولاد میشود.
خزش: در دماهای بالا، فولاد به آرامی تغییر شکل میدهد که به این پدیده خزش میگویند. خزش میتواند باعث تغییر شکل دائمی و در نهایت شکست سازه شود.
اکسیداسیون: در دماهای بالا، سرعت واکنشهای اکسیداسیون افزایش یافته و باعث تشکیل لایههای اکسیدی بر روی سطح فولاد میشود. این لایههای اکسیدی میتوانند ترد و شکننده باشند و مقاومت فولاد را در برابر تنش کاهش دهند.
تاثیر دماهای پایین بر فولاد
ترد شدن: با کاهش دما، فولاد ترد شده و مقاومت آن در برابر ضربه کاهش مییابد. این پدیده به ویژه در فولادهای کم آلیاژ و کربنی بیشتر مشاهده میشود.
کاهش چقرمگی: چقرمگی توانایی یک ماده در جذب انرژی قبل از شکست است. با کاهش دما، چقرمگی فولاد کاهش یافته و احتمال شکست ناگهانی افزایش مییابد.
عواقب آسیب دیدن فولاد بر اثر دما چیست؟
خزش و تغییر شکل دائمی: در دماهای بالا، فولاد به آرامی تغییر شکل میدهد و این میتواند منجر به تغییر ابعاد سازه، کاهش استحکام و در نهایت شکست شود.
کاهش مقاومت به خستگی: در دماهای بالا، مقاومت فولاد در برابر بارهای متناوب (خستگی) کاهش مییابد که این امر میتواند منجر به ترک خوردگی و شکست ناگهانی شود.
اکسیداسیون و زنگ زدگی: دماهای بالا سرعت واکنشهای اکسیداسیون را افزایش داده و باعث تشکیل لایههای اکسیدی بر روی سطح فولاد میشود. این لایهها میتوانند ترد و شکننده باشند و مقاومت فولاد را کاهش دهند.
تغییر در خواص مغناطیسی: برخی از فولادها در دماهای بالا خاصیت مغناطیسی خود را از دست میدهند که این امر میتواند بر عملکرد دستگاهها و تجهیزاتی که از این فولادها ساخته شدهاند تاثیر بگذارد.
عواقب دماهای پایین به شرح زیر است:
ترد شدن و افزایش شکنندگی: با کاهش دما، فولاد ترد شده و مقاومت آن در برابر ضربه کاهش مییابد. این امر به ویژه در دماهای بسیار پایین خطرناک است و میتواند منجر به شکست ناگهانی سازه شود.
کاهش چقرمگی: چقرمگی توانایی یک ماده در جذب انرژی قبل از شکست است. با کاهش دما، چقرمگی فولاد کاهش یافته و احتمال شکست ناگهانی افزایش مییابد.
تغییرات ابعادی: با تغییر دما، ابعاد فولاد نیز تغییر میکند که این امر میتواند باعث ایجاد تنشهای حرارتی در سازه شود.
عواقب آسیب دیدن فولاد بر اثر تغییرات دمایی ناگهانی (شوک حرارتی) چیست؟
ترک خوردگی حرارتی: تغییرات دمایی ناگهانی میتواند باعث ایجاد تنشهای حرارتی شدید در فولاد شود که این تنشها میتوانند منجر به ایجاد ترکهای حرارتی شوند.
کمانش: در برخی موارد، شوک حرارتی میتواند باعث کمانش اعضای سازهای شود.
خستگی حرارتی: تغییرات دمایی مکرر و ناگهانی میتواند باعث ایجاد خستگی حرارتی در فولاد شود که این امر میتواند به مرور زمان منجر به شکست شود.
- میزان رطوبت محیطی
رطوبت یکی از مهمترین عوامل محیطی است که بر خوردگی و در نتیجه طول عمر فولاد تأثیر مستقیمی میگذارد. رطوبت به عنوان یک محیط الکترولیتی عمل کرده و به واکنشهای شیمیایی که منجر به خوردگی میشوند، سرعت میبخشد.
تاثیر رطوبت بر فولاد به چه صورتی است؟
تشکیل سلولهای گالوانیکی: در حضور رطوبت، سطح فولاد به سلولهای گالوانیکی کوچکی تقسیم میشود که در آن برخی نقاط به عنوان آند (جایی که فلز اکسید میشود) و برخی دیگر به عنوان کاتد (جایی که اکسیژن کاهش مییابد) عمل میکنند.
حل شدن اکسیژن: رطوبت به اکسیژن اجازه میدهد تا در سطح فولاد حل شود و واکنشهای خوردگی را تشدید کند.
هدایت یونی: رطوبت به عنوان یک محیط رسانا عمل کرده و به یونهای حاصل از واکنشهای خوردگی اجازه میدهد تا در سطح فولاد سریع تر حرکت کنند.
عوامل تشدید کننده اثر رطوبت کدامند؟
وجود آلایندهها: نمکها، اسیدها، بازها و سایر آلایندهها میتوانند سرعت خوردگی فولاد را در حضور رطوبت به شدت افزایش دهند.
تغییرات دمایی: تغییرات دمایی مکرر باعث ایجاد تنشهای حرارتی در فولاد میشود که میتواند به ترک خوردگی و نفوذ رطوبت به داخل فلز کمک کند.
وجود نقاط تجمع رطوبت: نقاطی مانند گوشهها، درزها و شکافها که آب و رطوبت و حتی بخار آب در آنها جمع میشود، مستعد خوردگی هستند.
عواقب آسیب دیدن فولاد بر اثر رطوبت چیست؟
زنگ زدگی: شایعترین اثر رطوبت بر فولاد، تشکیل زنگ زدگی است. زنگ زدگی در واقع یک لایه اکسید آهن است که بر روی سطح فولاد تشکیل میشود و به تدریج به داخل فلز نفوذ میکند.
کاهش مقاومت مکانیکی: زنگ زدگی باعث کاهش ضخامت فولاد و ایجاد حفرههایی در آن میشود که در نتیجه مقاومت مکانیکی فولاد را کاهش میدهد.
تخریب پوششهای محافظ: رطوبت میتواند باعث تخریب پوششهای محافظ مانند رنگ و روکشهای فلزی شود و در نتیجه فولاد را در معرض مستقیم محیط خورنده قرار دهد.
افزایش سرعت خوردگی: رطوبت سرعت سایر انواع خوردگی مانند خوردگی حفرهای و خوردگی تنشی را نیز افزایش میدهد.
- میزان اسیدی یا قلیایی بودن محیط
pH شاخص اندازه گیری میزان اسیدی یا قلیایی بودن مواد می باشد که بین بازه 0 تا 14 تعریف شده که بازه ی 0 تا 6 بازه ی اسیدی بودن و 8 تا 14 بازه ی قلیایی بودن است و عدد 7 نشانگر خنثی بودن ماده می باشد. Ph محیط، یکی دیگر از عوامل مهمی است که به شدت بر سرعت و نوع خوردگی فولاد تاثیر میگذارد.
تاثیر pH بر فولاد به چه صورتی است؟
محیطهای اسیدی: در محیطهای اسیدی، یونهای هیدروژن (H+) غالب هستند. این یونها به شدت به آهن حمله کرده و باعث تشکیل یونهای آهن و آزاد شدن گاز هیدروژن میشوند. این فرآیند باعث تسریع فرایند خوردگی میشود.
محیطهای قلیایی: در محیطهای قلیایی، یونهای هیدروکسید (OH-) غالب هستند. این یونها با یونهای آهن واکنش داده و هیدروکسید آهن (زنگ زدگی) را تشکیل میدهند. اگرچه سرعت خوردگی در محیطهای قلیایی به اندازه محیطهای اسیدی نیست، اما باز هم میتواند به فولاد در مدت زمان طولانی آسیب جدی برساند.
عوامل تشدید کننده اثر pH
وجود یونهای کلر: یونهای کلر میتوانند باعث شکستن لایههای محافظ اکسیدی شده و سرعت خوردگی را افزایش دهند. یک نمونه ی بارز از این نوع خوردگی، آسیب دیدن میله های نگهدارنده و پلکان هایی است که داخل استخر ها وجود دارد. این پلکان ها و میله ها به مرور دچار خوردگی می شوند.
حضور سایر یونهای خورنده: یونهای سولفات، نیترات و سایر یونهای خورنده نیز میتوانند سرعت خوردگی را افزایش دهند.
تغییرات دما: تغییرات دما میتواند بر سرعت واکنشهای شیمیایی و در نتیجه بر سرعت خوردگی تاثیر بگذارد.
عواقب آسیب دیدن فولاد بر اثر pH چیست؟
افزایش سرعت خوردگی: در هر دو محیط اسیدی و قلیایی، سرعت خوردگی فولاد نسبت به محیط خنثی (pH=7) بیشتر است.
تغییر نوع خوردگی: نوع خوردگی نیز با تغییر pH تغییر میکند. به عنوان مثال، در محیطهای اسیدی، خوردگی یکنواخت رایجتر است، در حالی که در محیطهای قلیایی، خوردگی حفرهای بیشتر مشاهده میشود.
تخریب پوششهای محافظ: محیطهای اسیدی و قلیایی میتوانند پوششهای محافظ را تخریب کرده و فولاد را در معرض مستقیم محیط خورنده قرار دهند.
- وجود انواع آلاینده های طبیعی و شیمیایی
آلایندهها، مواد خارجی هستند که به طور طبیعی یا مصنوعی وارد محیط میشوند و میتوانند سرعت و نوع خوردگی فولاد را به شدت افزایش دهند. این آلایندهها میتوانند به شکل گاز، مایع یا جامد باشند.
تاثیر آلاینده ها بر فولاد به چه صورتی است؟
تغییر pH محیط: اکثر از آلایندهها میتوانند pH محیط را تغییر داده و محیط را اسیدی یا قلیایی کنند که هر دو این شرایط سرعت خوردگی را افزایش میدهند.
تشکیل سلولهای گالوانیکی: برخی از آلایندهها میتوانند با فولاد واکنش داده و سلولهای گالوانیکی ایجاد کنند که منجر به خوردگی موضعی میشود.
تخریب پوششهای محافظ: بسیاری از آلایندهها میتوانند پوششهای محافظ را تخریب کرده و فولاد را در معرض مستقیم محیط خورنده قرار دهند.
کاتالیزور برای واکنشهای خوردگی: برخی از آلایندهها میتوانند به عنوان کاتالیزور عمل کرده و سرعت واکنشهای خوردگی را افزایش دهند.
انواع آلایندهها و اثرات آن ها بر فولاد
نمکها: نمکها مانند کلرید سدیم (نمک طعام) میتوانند به شدت سرعت خوردگی را افزایش دهند. یونهای کلر میتوانند به داخل لایههای محافظ نفوذ کرده و باعث ایجاد حفرههای خوردگی شوند.
اسیدها: اسیدهای موجود در باران اسیدی، فاضلاب صنعتی و سایر منابع میتوانند به طور مستقیم به فولاد حمله کرده و باعث خوردگی و آسیب های جدی شوند.
بازها: بازهایی مانند آمونیاک میتوانند با برخی از آلیاژهای فولاد واکنش داده و باعث خوردگی شوند.
گازهای خورنده: گازهایی مانند دیاکسید گوگرد (SO2)، دیاکسید نیتروژن (NO2) و هیدروژن سولفید (H2S) میتوانند در حضور رطوبت با فولاد واکنش داده و باعث خوردگی شوند.
ذرات معلق: ذرات معلق در هوا مانند گرد و غبار، دوده و خاکستر میتوانند بر روی سطح فولاد نشسته و به عنوان کاتالیزور برای واکنشهای خوردگی عمل کنند.
عواقب آسیب دیدن فولاد بر اثر انواع آلاینده ها چیست؟
کاهش مقاومت مکانیکی: آلایندهها میتوانند باعث ایجاد حفرهها، ترکها و ضعیف شدن ساختار فولاد شوند که در نتیجه مقاومت مکانیکی آن را کاهش میدهد.
کاهش طول عمر: خوردگی ناشی از آلایندهها میتواند به تدریج ضخامت فولاد را کاهش داده و طول عمر آن را به شدت کاهش دهد.
افزایش هزینههای تعمیر و نگهداری: برای جلوگیری از خرابی کامل سازه، نیاز به انجام تعمیرات و نگهداری مداوم است که هزینههای زیادی را به دنبال دارد.
خطرات ایمنی: خوردگی ناشی از آلایندهها میتواند باعث ایجاد شکست ناگهانی سازه شده و خطرات جانی و مالی را به دنبال داشته باشد.
تخریب پوششهای محافظ: بسیاری از آلایندهها میتوانند پوششهای محافظ را تخریب کرده و فولاد را در معرض مستقیم محیط خورنده قرار دهند.
تغییر در ظاهر: خوردگی ناشی از آلایندهها میتواند باعث تغییر رنگ و ظاهر فولاد شود که از نظر زیباییشناسی مطلوب نیست.
- انواع تنش های مکانیکی
تنشهای مکانیکی یکی از مهمترین عوامل مؤثر بر طول عمر فولاد هستند. این تنشها میتوانند به دلایل مختلفی مانند بارگذاری، تغییر شکل، جوشکاری، برش و ... ایجاد شوند.
انواع تنشهای مکانیکی و تأثیر آنها
تنشهای کششی: این نوع تنشها باعث کشیده شدن فولاد میشوند و اگر از حد تحمل فولاد فراتر روند، باعث ایجاد ترک و نهایتا شکست میشوند.
تنشهای فشاری: این تنشها باعث فشرده شدن فولاد میشوند و اگر از حد تحمل فولاد فراتر روند، باعث تغییر شکل پلاستیکی و کاهش استحکام میشوند.
تنشهای برشی: این تنشها باعث لغزش لایههای فولاد نسبت به یکدیگر میشوند و اگر از حد تحمل فولاد فراتر روند، باعث ایجاد ترک و شکست میشوند.
تنشهای خستگی: تنشهای متناوب و تکراری میتوانند باعث ایجاد ترکهای خستگی در فولاد شوند و با گذشت زمان این ترکها گسترش یافته و به شکست منجر شوند.
تاثیر تنش های مکانیکی بر فولاد به چه صورتی است؟
توسعه ترکها: تنشهای مکانیکی میتوانند باعث ایجاد و گسترش ترکهای ریز در فولاد شوند. این ترکها با گذشت زمان و تحت تأثیر تنشهای تکراری بزرگتر شده و در نهایت به شکست منجر میشوند.
تغییر شکل پلاستیکی: تنشهای مکانیکی فراتر از حد الاستیک فولاد باعث تغییر شکل پلاستیکی دائمی میشوند که میتواند خواص مکانیکی فولاد را کاهش دهد.
خزش: در دماهای بالا و تحت بارگذاری ثابت، فولاد به آرامی تغییر شکل میدهد که به این پدیده خزش میگویند. خزش میتواند باعث ایجاد تغییر شکل دائمی و شکست شود.
عواملی که بر حساسیت فولاد به تنشهای مکانیکی تأثیر میگذارند
نوع فولاد: ترکیب شیمیایی فولاد، خواص مکانیکی آن را تعیین میکند و در نتیجه حساسیت آن به تنشهای مکانیکی متفاوت است.
عیوب ساختاری: وجود عیوب ساختاری مانند ناخالصیها، حفرهها و ترکهای ریز در فولاد میتواند حساسیت آن به تنشهای مکانیکی را افزایش دهد.
شرایط محیطی: رطوبت، دما و وجود مواد شیمیایی خورنده میتوانند بر مقاومت فولاد در برابر تنشهای مکانیکی تأثیر بگذارند.
نوع بارگذاری: نوع بارگذاری (ثابت، متناوب، شوک) و سرعت اعمال بار بر روی حساسیت فولاد به تنشهای مکانیکی تأثیر میگذارد.
عواقب آسیب دیدن فولاد بر اثر تنش های مکانیکی چیست؟
تنشهای مکانیکی علاوه بر ایجاد تغییر شکل و کاهش استحکام، عواقب جدی دیگری نیز بر طول عمر فولاد دارند که در ادامه به برخی از آنها اشاره میکنم:
شکست ناگهانی: در صورت اعمال تنشهای بیش از حد، فولاد ممکن است به طور ناگهانی و بدون هیچگونه نشانه قبلی بشکند. این امر میتواند منجر به خسارات جانی و مالی فراوانی شود.
خستگی: تنشهای متناوب و تکراری باعث ایجاد ترکهای خستگی میشوند که به مرور زمان گسترش یافته و در نهایت به شکست منجر میشوند.
کاهش قابلیت اطمینان سازه: تنشهای مکانیکی میتوانند باعث کاهش قابلیت اطمینان سازه شده و احتمال خرابی آن را افزایش دهند.
افزایش هزینههای تعمیر و نگهداری: برای جلوگیری از شکست سازه، نیاز به انجام بازرسیها و تعمیرات دورهای است که هزینههای زیادی را به دنبال دارد.
کاهش عمر مفید سازه: تنشهای مکانیکی میتوانند به طور قابل توجهی عمر مفید سازه را کاهش دهند.
- تابش نور مستقیم خورشید
تابش خورشید نیز یکی از عوامل مهمی است که بر طول عمر فولاد تأثیر میگذارد. انرژی حرارتی ناشی از تابش خورشید و تغییرات دمایی ناشی از آن، باعث ایجاد تنشهای حرارتی و تسریع فرایندهای خوردگی در فولاد و کاهش طول عمر مفید فولاد میشوند.
تاثیر نور مستقیم خورشید بر فولاد به چه صورتی است؟
تنشهای حرارتی: تغییرات دمایی ناشی از تابش خورشید باعث انبساط و انقباض فولاد میشود. اگر این تغییرات دمایی به صورت ناگهانی یا مکرر رخ دهند، تنشهای حرارتی در فولاد ایجاد شده و منجر به ایجاد ترکها و تغییر شکل در آن میشود.
خوردگی ناشی از حرارت: دمای بالای ناشی از تابش خورشید میتواند سرعت واکنشهای خوردگی را افزایش دهد. به ویژه در محیطهای مرطوب، ترکیب حرارت و رطوبت باعث تشدید خوردگی میشود.
تخریب پوششهای محافظ: تابش مستقیم خورشید میتواند باعث تخریب پوششهای محافظ مانند رنگ و روکشهای فلزی شده و فولاد را در معرض مستقیم عوامل محیطی قرار دهد.
عواقب آسیب دیدن فولاد بر اثر نور مستقیم خورشید چیست؟
کاهش مقاومت مکانیکی: تنشهای حرارتی و خوردگی ناشی از تابش خورشید میتوانند باعث کاهش مقاومت مکانیکی فولاد شوند.
تغییر شکل: تغییرات دمایی مکرر باعث ایجاد تغییر شکل دائمی در فولاد میشود.
کاهش طول عمر: تابش خورشید میتواند به طور قابل توجهی عمر مفید سازههای فولادی را کاهش دهد.
افزایش هزینههای تعمیر و نگهداری: برای جلوگیری از خرابی سازه، نیاز به انجام تعمیرات و نگهداری دورهای است که هزینههای زیادی را به دنبال دارد.
جمع بندی و نتیجه گیری
با توجه به مواردی که گفته شد، مواردی که در کاهش طول عمر مفید فولاد را نام برده و اثرات هر کدام بر روی خواص فیزیکی فولاد را بررسی کردیم. اکنون ما با شناخت این عوامل، میتوانیم درک بهتری از چگونگی محافظت و افزایش طول عمر سازهها پیدا کنیم و از سرمایههای خود به نحو احسن بهرهبرداری نماییم. مشاورین و متخصصین شرکت سافا همواره در کنار شما بوده و برای کسب نتایج درخشان پروژه های عمرانی و صنعتی شما، با شما همراه می شوند و با ارائه راهنمایی های تخصصی و فنی، به ساخت رویاهای شما جامه ی عمل می پوشانند. شما می توانید برای دریافت مشاوره ی رایگان با متخصصین و مشاورین سافا روی لینک مربوطه کلیک نمایید و دغدغه های خود را با ما در میان بگذارید.