سیستم های جوش و سیر تكامل آن
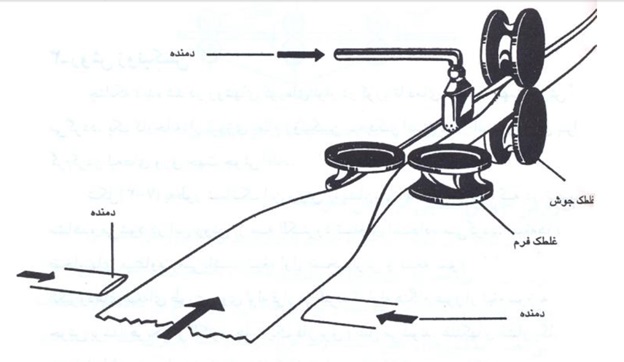
همانگونه كه در فصول قبلی شرح آن گذشت، در فرآیند تولید لوله و پروفیل فولادی، جهت تولید لوله و بسیاری از انواع پروفیل ها موسوم به پروفیل های بسته، لازم است دولبه ورق در نقطه تماس به یكدیگر جوش داده شوند. بنا به اهمیت موضوع در این فصل به شرح بعضی از روش های جوش مورداستفاده در این رابطه می پردازیم.
1_ جوش شعله ای یا كوره ای
با كشف گاز روشنایی درسال 1815 در انگلستان توسط ویلیام موردوك كوشش شد لوله ازطریق آهنگری تولید و با كمك كوره گازی جوش داده شود. در سال 1825 یك تاجر آهن به نام جیمز ویت هاوس موفق به ثبت روش خود در تولید لوله درزجوش گردید. او یك نوار آهن با عرض معین را با چكش كاری بر روی یك سنبه و یا به وسیله یك قالب به صورت لوله فرم داد. سپس ابتدا نیمی از لوله را در یك كوره شعله ای تادمای جوش «1300 تا 1400 درجه سانتیگراد» گرم نمود و یك سر آن را با كمك انبر كشش از قالب كشش یك دستگاه كشش زنجیری رد نمود و از این طریق توانست دو لبه را به هم جوش دهد. پس از سرد شدن نیم دیگر لوله نیز به همین روش ساخته شد.
در این روش قالب از دو نیمه ساخته شده بود. هنگام عبور قسمت سرد، قالب، عبور بدون فشار قطعه را امكان پذیر می ساخت ولی هنگام عبور قسمت گرم فشار زیادی را به لوله وارد می نمود تا دو لبه به هم جوش شود.
در سی سال اول پس از كشف روش جیمز ویتهاوس قدم به قدم در انگلستان پیشرفت هایی برای روش فوق پیشنهاد و به اجرا گذاشته شد، چنانكه درسال 1852 این روش به نقطه اوج خود رسید. در شكل (1-7) این روش به طور شماتیك به تصویر درآمده است. امروزه هنوز این روش در برخی از كشورها مورد استفاده قرار می گیرد.
شكل (1-7) : شماتیك روش جوش كورهای
انگلیسی ها سال ها روش تولید لوله را مخفی نگه داشته و به این ترتیب انحصار تولید لوله را در جهان سال ها در اختیار داشتند. اما در سال 1846 آلبرت پونسگن در منطقه غرب آلمان كارگاهی برای ساخت لوله باهمان روش تأسیس نمود كه در سال 1849 به بهره برداری رسید.
2_ روش فریتس مون
تكامل تولید لوله جوشی در سال 1931 و به وسیله یك امریكایی به نام فریتس مون كامل گردید. او توانست ازطریق جوش كوره ای، لوله را از نوارهایی با طول زیاد تولید نماید. با این روش تولید لوله تا قطر خارجی 3/114 میلی متر یعنی 4 اینچ قابل تولید بود.
همانگونه كه در شكل (2-7) دیده می شود نوار پس از گرم شدن در كوره از یك سری غلتك های افقی و عمودی جهت فرم دهی و غلتك های فشاری جهت جوش دو لبه عبور داده می شود. قبل از ورود لوله به درون غلتك ها دولبه با كمك دمنده هایی تا نقطه جوش حرارت داده می شوند. اختلاف دمای بین دو لبه و بقیه عرض نوار امكان افزایش فشار و در نتیجه جوش بهتر و تولید تمیزتر را فراهم می نماید
شكل (2-7) : شماتیك روش فریتس مون
یك خط تولید به روش فریتس مون تشكیل شده است از تجهیزات جوش لب به لب نوار، یك انباره جهت ذخیره كردن نوار و جلوگیری ازتوقف خط به هنگام جوش دو نوار، یك كوره عبوری كه نوار با عبور از آن تا دمای جوش گرم می گردد و بالاخره غلتك هایی كه در بالا به آنها اشاره شد. در خطوط جدید پس از جوش دو لبه و تولید لوله با قطر خارجی معین از یك سیستم كشش غلتكی نیز استفاده می كنند تا لوله های با قطر پایین تر به راحتی تولید شود.
كارگاه های زیادی در سطح جهان هنوز از روش فریتس مون جهت تولید لوله آب و گاز استفاده می كنند. این روش بسیار اقتصادی بوده و راندمان بالایی دارد اما از این روش نمی توان در تولید لوله های با كیفیت كه در دیگ های بخار و نظایر آن به كار می روند استفاده كرد.
3_ روش زونیكسن
چنانكه دیده شد در روش های كوره ای نوار در كوره تا دمای مناسب جهت جوش گرم می گردد. یك كارخانه دار نروژی به نام زونیكسن به فكر استفاده از انرژی برق برای گرم كردن لبه های ورق جهت جوش افتاد.
شكل (3-7) به طور شماتیك این روش را نشان می دهد. همانگونه كه در تصویر مشاهده می شود در این روش از سه الكترود تیغه ای استفاده می گردد. تیغه ها دارای ضخامت های متفاوت می باشند. تیغه اول ضخیم ترین و تیغه سوم نازك ترین آن است. الكترودهای تیغه ای طوری روی لوله قرار می گیرند كه لوله هنگام عبور از تیغه سوم به گرمای جوش برسد. هریك از الكترودها به یك فاز برق وصل می شوند. غلتك های فشار به كار رفته باید از لحاظ برقی عایق شوند. این غلتك ها نه تنها به عنوان غلتك جوش بلكه همچنین به عنوان غلتك محرك لوله نیز مورداستفاده قرار می گیرند. با وجودی كه نقطه تمركز گرما در لبه های درز لوله قرار دارد ولی به علت هدایت گرمایی حرارت در كل سطح مقطع لوله پراكنده می شود.
روش زونیكسن در سال 1928 به ثبت رسید و از آن سال تاكنون تعداد زیادی كارگاه لوله سازی با این روش بكار پرداخته اند كه هنوز نیز تعدادی از آنها به كار گرفته می شوند.
شكل (3-7) : شماتیك روش زونیكسن
4_ روش جوش القایی فركانس متوسط
از سال 1965 درز لوله را با كمك جریان برق و با روش القایی با فركانس بین 4 تا 10 كیلوهرتز جوش می دهند. در این روش جریان برق با كمك یك سری ایندكتور خطی به درز لوله و بدون تماس با آن انتقال داده شده و گرمای حاصل را جهت جوش لبه ها مورد استفاده قرار می دهند. ایندكتورهای خطی پشت سرهم قرار گرفته و بسته به توان خط تا نیم متر فاصله را در بر می گیرند. جهت راندمان خوب، این اندكتورها خیلی نزدیك لبه های لوله كار گذاشته می شوند. ازطریق القا و به خاطر بالا بودن دانسیته توان مقدار زیادی انرژی در زمانی كوتاه به لبه های لوله منتقل شده و به علت اثر پوستی مقدار زیادی گرما در فاصله كمی از لبه به وجود می آید انتخاب فركانس و توان، به ضخامت لوله و سرعت خطی تولید بستگی دارد و از رابطه ژول(P=R.I2) به دست می آید
در یك خط جوش با این روش یك ژنراتور فركانس متوسط با كمك یك ترانسفورماتور با خازن های موازی جریان لازم را به وجود آورده و به وسیله ایندكتور به لبه های لوله القا می كند. لبه های درز لوله به عمق 5 تا 10 میلیمتر تا دمای جوش گرم می شوند كه با فشار حاصل از غلتك های جوش به هم جوش می گردند.
شكل (4-7) به طور شماتیك تجهیزات جوش لوله با روش القایی فركانس متوسط با دو ایندكتور را نشان می دهد.
.
شكل (4-7) : شماتیك روش جوش القایی فركانس متوسط
5_ روش جوش گازی
در این روش گرمای لازم برای جوش از سوختن مخلوط گاز و هوا به دست می آید.
در سال های اولیه استفاده از این روش از گاز هیدروژن استفاده می گردید ولی با كشف گاز استیلن این گاز به جای هیدروژن به كار گرفته شد.
سوختن گاز استیلن با اكسیژن حرارتی معادل 3100 درجه سانتیگراد تولید می نماید. گاز استیلن از تركیب كاربید كلسیم و آب به دست می آید.
اولین جوش با این روش در حدود سال های 1910 ساخته شد. در آن زمان تنها پِیك جوشكاری تك شعله وجود داشت. خط تولید از یك خط فرمینگ كه وظیفه تغییر فرم نوار گرم یا سرد را به عهده داشت به همراه یك پیك جوشكاری تشكیل می شد. با پیدایش پیك های چند شعله (تا 16 شعله) خط لوله سازی نیز تكمیل گردید. در كنار میز فرمینگ میز جوش و سپس میز سایزینگ و بالاخره اره اضافه شد. شكل (5-7) به طور شماتیك تجهیزات یك خط لوله سازی با این روش را نشان میدهد
شكل (5-7) : شماتیك روش جوش گازی
پنج جفت غلتك فرمینگ وظیفه فرم دادن نوار را به صورت لوله درزدار به عهده دارد. به دنبال آنها دو جفت غلتك فشار وظیفه نزدیك كردن درز لوله به هم را دارد، تا پس از گرم شدن لبه ها با كمك پیك چند شعله دو لبه به هم جوش شود. به دنبال آنها دوجفت غلتك سایزینگ جهت سایز كردن لوله و در بین آنها یك غلتك تابگیر برای تابگیری به كار رفته است
در آغاز استفاده از این سیستم جوش، تولید متناسب با طول نوار عملی بود. اما بعدها با جوش دادن لب به لب چند نوار امكان تولید پیوسته فراهم گردید.
استفاده از این سیستم جوش امروزه در مقیاس بسیار كمی متداول بوده و جای خود را به سیستم جوش برقی داده است.
6_ جوش مقاومت الكتریكی با فركانس پایین
درسال 1856 فیزیكدان انگلیسی جیمز ژول رابطه میان مقاومت اصطكاكی و گرما را كشف نمود كه به گرمای ژول معروف است. طبق این نظریه چیرگی بر مقاومت اصطكاكی در یك جسم كه از آن جریان برق عبور می كند گرما تولید می نماید. میدان الكتریكی، كاری معادل QU با توان ρ= U.Q/t=U.I=R.I2انجام می دهد.
درسال 1877 یك مربی جوان دانشگاه به نام مهندس الیهیو تامسون مجدداً این پدیده را مدنظر قرار داد و به این نتیجه رسید كه می توان از گرمای حاصل در یك مقاومت الكتریكی برای جوشكاری استفاده كرد.
درسالهای بین 1886 تا 1890 تامسون روش هایی را در مورد جوشكاری الكتریكی فلزات به ثبت رسانید. درسال 1898 او اولین دستگاه جوش برقی و اولین ترانس جوش را در جهان ساخت. در همین سال شركت " استاندارد تول" در شهر كلیولند ایالت اوهایو امریكا روشی را به ثبت رسانید كه از سیستم جوش مقاومتی برای جوش و تولید لوله استفاده میشد.
در روش استاندارد تول دو الكترود مجزا از هم در كنار غلتك های فشار با لبه های لوله درزدار در تماس قرار گرفته جریان برق را به لبه های لوله منتقل می نمایند. شكل (6-7) به طور شماتیك این روش را نشان میدهد
.
شكل (6-7) : شماتیك روش جوش الكتریكی
روش جوش مقاومت الكتریكی در ایالات متحده و سپس در آلمان تحرك زیادی در صنعت لوله سازی از ورق گرم به صورت پیوسته ایجاد نمود. مشكل اصلی در این روش هدایت دقیق لبه های لوله به زیر الكترودها است. پیش فرض جوش مطلوب در این روش ورق خوب نورد شده با تلرانس عرض و ضخامت بسیار كم است. این روش هنوز هم مورد استفاده قرار می گیرد
7_ روش كانداكتیو(روش جوش مقاومتی فركانس بالا )
روش جوش مقاومتی با انتقال توان به وسیله كنتاكت با فركانس تا 450 كیلوهرتز در سال 1956 به وسیله شركت New Rochell Tool Corp و تحت نام "ترماتول" اجرا گردید. چنانكه در شكل (7-7) دیده می شود در این روش جریان فركانس بالا ازطریق دو كنتاكت به لبه های لوله منتقل می گردد. در فركانس بالا میدان متناوب مغناطیسی تأثیر زیادی روی عبور جریان ها می گذارد، طوری كه این جریان ها را می توان در مسیرهای خاصی
هدایت نمود
شكل (7-7) : شماتیك روش جوش فركانس بالا با كنتاكت
مشخصه اصلی جریان های فركانس بالا در تأثیر پوستی است. تحت این عنوان چنین فهمیده می شود كه جریان در یك هادی مثلاً یك میله با افزایش فركانس تحت اثر القاء همواره هرچه بیشتر به سمت سطح خارجی رانده می شود، درحالیكه جریان مستقیم از تمام سطح هادی عبور می كند. در جریان متناوب شدت جریان با افزایش فركانس در داخل هادی كم شده و در سطح خارجی بر عكس افزایش می یابد.
تأثیری معادل "اثرپوستی" در جریان فركانس بالا (تحت تأثیر القا) "اثر كشش متقابل" است، و از این واقعیت سرچشمه می گیرد كه جریان های فركانس بالایی كه از دو هادی نزدیك به هم و در خلاف جهت یكدیگر عبور می نمایند یكدیگر را جذب می كنند. اجرای این پدیده در روش جوش فركانس بالا با كنتاكت نتیجه زیر را به دست می دهد
جریان فركانس بالا در یك قشر نازك یك كنتاكت عبور نموده از آنجا به لبه درز لوله انتقال می یابد و در نقطه اتصال این لبه (نقطه جوش) لبه لوله را دور زده از لبه دیگر به كنتاكت دیگر برمی گردد. در اثر پدیده جذب جریان های مختلف الجهت قسمت اعظم این جریان ها از قشر نازك لبه لوله و نه از پیرامون آن عبور می نماید. در اثر عبور این جریان، گرما نیز در لبه نازك لوله ایجاد می شود كه به علت مقاومت اهمی بالا در نقطه جوش تمركز گرما تا حد رسیدن به درجه حرارت جوش در این نقطه به وجود می آید.
به علت عبور جریان از پوسته، مقاومت واقعی برای جریان فركانس بالا تا 50 برابر بیشتر از سیستم جوش مقاومتی با فركانس پایین است، درنتیجه جریان لازم برای جوش در آن 20/1 تا 50/1 برابر جریان لازم درجوش فركانس پایین است. بنابراین در این روش سرعت جوش به مقدار قابل ملاحظه ای قابل افزایش است و زمان جوش آنقدر كوتاه است كه خطری متوجه لوله نمی شود. به همین خاطر از این سیستم نه تنها برای موادی كه قابلیت جوشكاری خوبی دارند، بلكه در مورد موادی كه قابلیت جوشكاری كمی دارند و حتی فلزات غیرآهنی می توان استفاده نمود.
8_ سیستم اندوولد (جوش مقاومتی فركانس بالا به صورت ایندكتیو )
امكان انتقال جریان فركانس بالا ازطریق القا جهت جوش درز لوله سال هاست كه شناخته شده است. اولین ثبت این روش به سال 1930 مربوط می شود. در دهه 50 این روش به خصوص در امریكا مورد استفاده قرار گرفت . در دهه 70 شركت مانسمان با كمك شركت زیمنس این روش را به وسیله یك ترانس كه برق با فركانس 450 كیلوهرتز تولید می نمود در سیستم های جوش لوله مورد استفاده قرار داد. جریان فركانس بالا در این روش توسط یك لامپ اسیلاتور تولید و از طریق یك سیم پیچ به نام ایندكتور كه در دور لوله قرار می گرفت به آن القا می گردید. جریان القایی از لبه لوله در دو جهت پیرامون و درز تا محل اتصال دو لبه عبور نموده سپس در خلاف جهت برمی گردد. گرمای حاصل در این سیستم همانند سیستم جوش فركانس بالا با كنتاكت، در لبه درز لوله متمركز می شود. مزیت این سیستم نسبت به سیستم جوش با كنتاكت در انتقال و یا به عبارت بهتر القاء جریان بدون تماس است كه درنتیجه در روی لوله اثر تماس باقی نمی ماند و ایندكتور نیز سایش نمی یابد. بدین جهت از این سیستم برای تولید لوله با كیفیت بالا می توان استفاده كرد
شكل(8-7) سیستم جوش فركانس بالا با ایندكتور را به طور شماتیك نشان می دهد
شكل (8-7) : شماتیك روش جوش فركانس بالا با اندكتور
9_ روش جوش با قوس آرگون
در طول جنگ جهانی دوم در ایالات متحده امریكا روش جدید جوش قوس الكتریكی كشف شد كه جهت جوش فلز منیزیم در صنایع هواپیما سازی مورد استفاده قرار گرفت. این روش بعدها در سایر كشورها مورد استفاده قرار گرفته و برای جوش كلیه فلزات غیر آهنی و فولادهای آلیاژی استفاده شد.
جوش قوس آرگون برای فولادهای آستنیتی به خوبی قابل استفاده است. آرگون به عنوان گاز محافظ، از ورود اكسیژن و هیدروژن در محل جوش جلوگیری نموده مانع از ایجاد سرباره و به خصوص سرباره كروم می گردد. جوش قوس آرگون به ویژه برای جوش لوله های با ضخامت كم از فلزات فوق الذكر بسیار مناسب است. در این روش گرما در اثر قوس الكتریكی بین الكترود كه از جنس تنگستن است و درز لوله به وجود می آید و وجود گاز آرگون محافظ خوبی برای جلوگیری از ورود ناخالصی در محل جوش می شود
شكل (9-7) یك دستگاه اتوماتیك جوش آرگون را نشان می دهد. در این روش می توان هم از برق مستقیم و هم از برق متناوب استفاده كرد. استفاده از برق متناوب با فركانس زیاد امكان جوش لوله از تمامی فلزات و با ضخامت حتی كمتر از 1 میلیمتر را به خوبی فراهم می سازد. سرعت زیاد و منطقه كوچك جوش باعث كم شدن خطر تغییر شكل و ترك خوردگی می شود. این روش در جوش فولادهای آلیاژی به خوبی قابل استفاده است.
شكل(9-7) : شماتیك روش جوش با قوس آرگون
10_ روش جوش زیر پودر
حدود 50 سال است كه روش جوش زیر پودر شناخته شده می باشد. این سیستم در اصل و از لحاظ اصول فیزیكی همانند جوش قوس الكتریكی است با این تفاوت كه در این روش ذوب شدن محل جوش توسط قوس الكتریكی در زیر پودر صورت می گیرد. پودر قبلاً در محل درز لوله آماده جوش ریخته می شود. الكترود جوشكاری را یك مفتول صاف و بدون پوشش تشكیل می دهد كه باسرعت ثابت حركت می كند.
شكل (10-7) به طور شماتیك كلیه تجهیزات یك دستگاه جوش زیر پودر را نشان می دهد. از یك قیف مخصوص پودر به درز لوله ریخته می شود. سیم جوش از یك مخزن با كمك غلتك های هدایت كننده به نازل جوش حمل می گردد. در آنجا جریان برق به وسیله یك كنتاكت اصطكاكی به سیم جوش منتقل میشود. پودر استفاده نشده از محل جوش مكیده شده و جمع آوری می گردد
این روش جوش برای جوش طولی و اسپیرال، لوله های بزرگ از 500 الی 1200 میلیمتر قطر خارجی مورد استفاده قرار می گیرد
شكل (10-7) : شماتیك روش جوش زیرپودر