كلیاتی در مورد فولاد
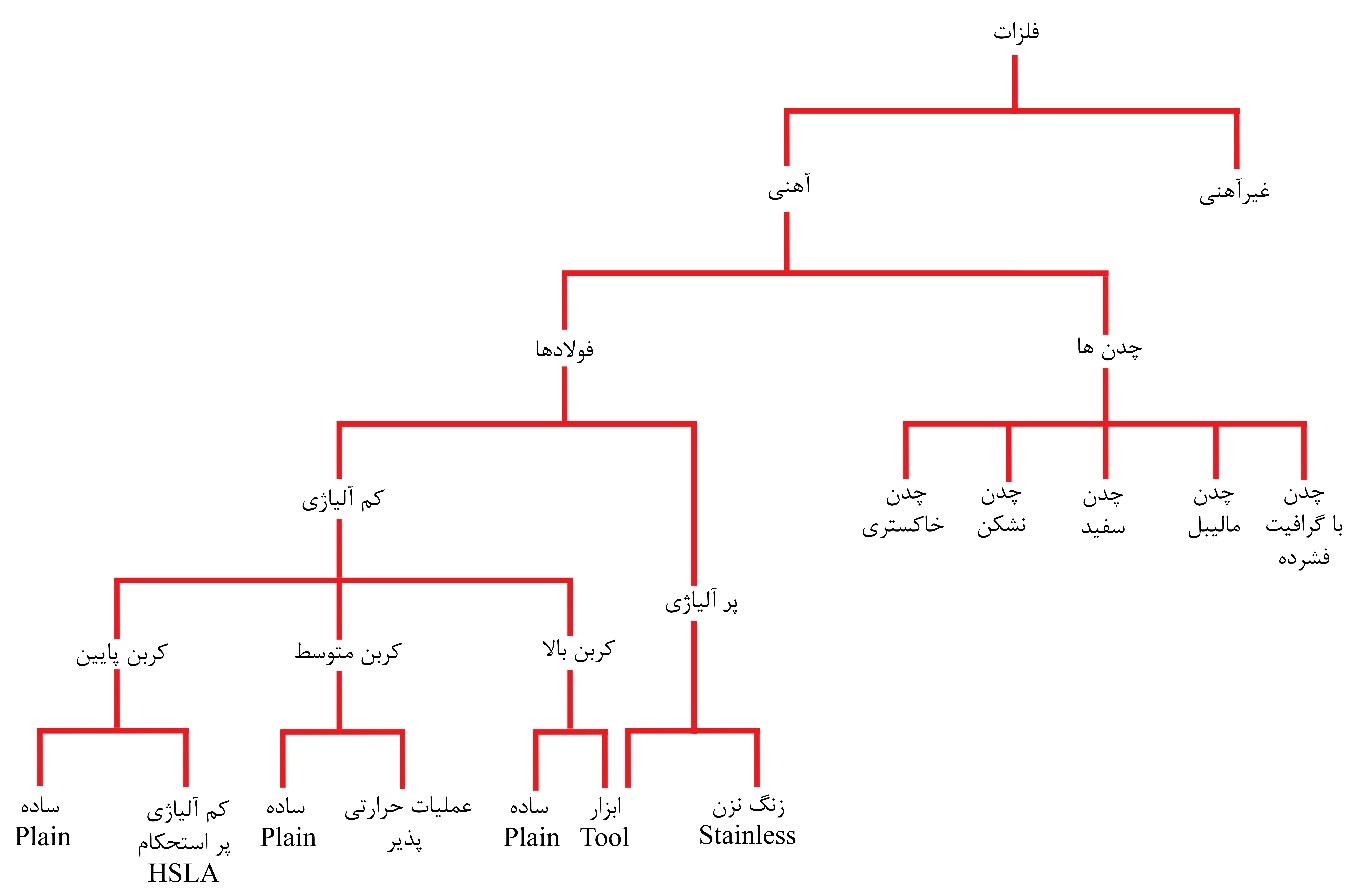
عامل مؤثر در كاربرد فراوان لوله و پروفیل فولادی، آلیاژهای مختلف آهنی است كه اهمیت آن در نگاهی به فرآیندهای تولید فولاد، رشد و شكل گیری آن در جهان و نیز خواص منحصر به فرد این موهبت الهی روشن خواهد شد.
از این رو در این فصل به تعریف فولاد به عنوان ماده اولیه ساخت پروفیل و نیز روش های مختلف تولید آن پرداخته می شود.
1- تعریف فولاد
فولاد به انواع بیشماری از آلیاژها گفته می شود كه عنصر اصلی آنها را آهن تشكیل می دهد و كربن به عنوان مهمترین ماده آلیاژی آن محسوب می گردد.
میزان كربن موجود در فولاد بین 03/0 تا 5/1 درصد متغیر است و در موارد معدودی نیز به 25/2 درصد می رسد. آلیاژهای آهنی كه كمتر از 03/0 درصد كربن داشته باشند، آهن نامیده می شوند. آلیاژهایی كه بیش از 5/1 درصد كربن دارند، عموما چدن نامیده می شوند و فرم خام آن را نیز آهن خام می نامند.
آلیاژی كه كمتر از 50 درصد آهن داشته باشد، فولاد نامیده نمی شود.
2- طبقه بندی فولاد
فولاد را می توان به طرق گوناگونی طبقه بندی كرد. معیار اولیه جهت طبقه بندی فولاد به كمك آنالیز شیمیایی آن صورت می گیرد. اكثر كشورهای عمده جهان در طبقه بندی فولاد، روش خاص خویش را بكار بسته و آن را بر مبنای میزان كربن، منگنز، فسفر، سولفور و یا سیلیسیوم موجود در آن طبقه بندی می نمایند.
به طور كلی در مقیاس وسیع، تقسیم بندی ذیل را داریم:
2- الف- فولاد كربنی
كربن، ارزانترین و در عین حال مؤثرترین عامل آلیاژی در فولاد است. نوع فولاد با كربن كم، بین 08/0 تا 15/0درصد كربن دارد كه بیشتر هنگامی مورد استفاده قرار می گیرد كه هزینه كم، سطح نسبتاً خوب، دوام و سختی مطلوب ،قابلیت جوش پذیری و شكل پذیری و سهولت در كاركردن با آن موردنظر باشد. به عنوان مثال در مورد انواع ورق فولادی مورد استفاده بدنه اتومبیل، انواع لوله درزجوش، كانتینرهای فولادی و انواع سیم، از این نوع فولاد (دارای كربن كم) استفاده می شود.
نوع فولاد با كربن نسبتاً معتدل كه بین 15/0 تا 25/0 درصد كربن دارد، به راحتی در كارهای ساختمانی در ساختن پل ها، بدنه كامیون، وسایل راه آهن و غیره مورد استفاده قرار می گیرد.
نوع فولاد با كربن متوسط كه بین 25/0 تا 35/0 درصد كربن دارد، سخت تر و محكم تر از فولاد قبلی بوده و برای ساختن انواع لوله های بزرگ، بدنه كشتی، شفت و قسمت های مختلف ماشین آلات بكار می رود. نوع فولاد با كربن بین 35/0 تا 65/0 درصد، جهت ساختن انواع ماشین آلات سنگین بكار می رود.
ریل فولادی و انواع چرخ فولادی كه به استحكام زیاد و عكس العمل خوب در مقابل حرارت نیاز دارد، از فولادی تهیه میشود كه بین 65/0 تا 85/0 درصد كربن دارد. این نوع فولاد در مقابل حرارت، عكس العمل مساعدی نشان می دهد. فولاد با كربن بین 85/0 تا 2/1 درصد برای ساختن انواع فنر، ماشین آلات برش و مته های مخصوص صخره ها، مورد استفاده قرار می گیرد.
لازم به ذكر است نوع فولاد با كربن معمولی، بیشترین حجم تولید از انواع مختلف فولاد را در جهان حائز می باشد.
2- ب- فولاد آلیاژی
هنگامی كه از مواد آلیاژی گوناگونی استفاده شود، انواع بیشماری از تركیبات فولاد، قابل حصول است. مواد آلیاژی می توانند به تنهایی و یا به صورت تركیبی، مورداستفاده قرار گیرند. به طور كلی چنین نتیجه گرفته شده است كه تركیب مواد آلیاژی، هم از نقطه نظر هزینه و همچنین خصوصیات آنها، نسبت به استفاده از یك آلیاژ منحصر به فرد، برتری دارد. مهمترین فلزات آلیاژی به قرار ذیل هستند:
2- ب- 1- نیكل و كروم
نیكل و كروم مهمترین مواد آلیاژی فولاد هستند. نیكل در هیدروكسید آهن (Ferrite) حل گردیده و سبب افزایش استحكام فولاد می شود اما به سختی فولاد نمی افزاید. به دلیل مذكور و به دلیل هزینه آن، مدت زمانی است كه نیكل به عنوان تنها ماده آلیاژی، مورد استفاده همه جانبه قرار نمی گیرد. استفاده از مقدار كمی كروم، سبب افزایش قابلیت سخت شدن فولاد به كمك حرارت میشود و درمیزانی بیش از 5 درصد، مقاومت فولاد را در مقابل فرسایش و زنگ زدگی شدت می بخشد.
فولاد كربنی علاوه بر داشتن كربن، دارای حداكثر 65/1 درصد منگنز و احتمالاً مقادیر نسبتاً كمی نیز سیلیسیوم، آلومینیوم، مس و غیره می باشد. به طور كلی موارد استفاده فولاد كربنی در ساخت بدنه اتومبیل، لوازم منزل ،انواع ماشین آلات، كشتی، انواع كانتینرها و اسكلت ساختمان ها است . فولاد با آلیاژ كم نیز دارای 1 تا 5 درصد از مواد آلیاژی معمولی نظیر نیكل، كروم، مولیبدنوم ،تنگستن، تیتانیوم، نیوبیوم و غیره می باشد. اغلب در مواردی كه احتیاج به خصوصیات و كیفیات ویژه ای است و درعین حال، مسأله هزینه نیز مشكل عمده ای به حساب می آید، از این نوع فولاد استفاده می شود. این نوع فولاد در ساخت لوازم مخصوص فرود هواپیما، انواع شفت، انواع ابزار دستی، انواع چرخ دنده و بالاخره انواع فولاد تأسیساتی با استحكام زیاد بكار می رود.
فولاد با آلیاژ زیاد، حداقل دارای بیش از 5 درصد، از یكی از مواد آلیاژی است. این ماده آلیاژی عموماً كروم، نیكل، منگنز، مولیبدنوم و یا تنگستن می باشد. باید دانست كه فولاد ضدزنگ، خود نوع عمده ای از فولاد با آلیاژ زیاد بوده و معمولاً به فولادی اطلاق می گردد كه بیش از 5 درصد كروم داشته باشد. فولاد ضدزنگ به خاطر مقاومت در برابر سایش و استقامت در برابر زنگ زدگی ونیز ظاهر خوب آن، كاربرد فراوانی یافته است.از فولاد ضدزنگ در ساخت قطعات موتور جت، وسایل و لوازم شیمیایی، كارد و چنگال، انواع لوازم پخت و پز و بالاخره انواع دستگاه های مخصوص برش استفاده می شود.
كروم و نیكل در اغلب موارد توأماً مورد استفاده قرار می گیرند یا با مقادیر كمی وانادیوم، مولیبدنوم و یا بورون تركیب شده و به كار گرفته می شوند.علت بكارگیری توأم كروم و نیكل، كمك به افزایش میزان استحكام و همچنین قابلیت سخت شدن فولاد است. سایر موارد مذكور در فوق نیز به این روند كمك نموده و درعین حال، میزان احتیاج به نیكل و كروم را كاهش می دهند.
2- ب- 2- منگنز
منگنز درتمام انواع فولاد مورد استفاده قرار می گیرد. دلیل آن نیز كمك به افزایش قابلیت تأثیر حرارت بر فولاد است. وقتی میزان آن از یك درصد نیز بیشتر گردد، خود به عنوان یك ماده آلیاژی شناخته می شود.
2- ب- 3- وانادیوم، مولیبدنوم و بورون
اهمیت وانادیوم به دلیل خاصیت ضد اكسید كنندگی آن می باشد یعنی در تأثیر اكسیژن بر آهن و در نتیجه اكسیده شدن آهن می كاهد. مولیبدنوم و بورون نیز از مواد آلیاژی پرارزش هستند.
بكارگیری 0005/0 درصد بورون سبب میگردد تا احتیاج به كروم و مولیبدنوم ، حدوداً 50 درصد كاهش یابد ولی درعین حال استحكام و سختی موردنظر حفظ شود.
استفاده گسترده از بورون برای نخستین بار در جنگ جهانی دوم صورت گرفت (زمانی كه صرفه جویی هرچه بیشتر در مواد آلیاژی كمیاب موردنظر بود) و از آن دوره به بعد نیز استفاده از بورون ادامه یافت.
3- انواع محصولات فولادی
محصولات فولادی به 2 گروه عمده فولادهای كارنشده و فولادهای كارشده تقسیم می شوند. فولادهای كارنشده محصولات اولیه فولاد نظیر شمش، اسلب ،بلوم و بیلت و فولادهای كارشده، محصولات ثانویه فولاد از قبیل ورق، تیرآهن ،پروفیل، ناودانی، میلگرد لوله، نبشی و ستونی میباشند. درحقیقت ،مصرف كنندگان محصولات كارنشده فولاد، تولیدكنندگان محصولات كارشده فولاد هستند.
3- الف- محصولات كارنشده فولادی
منظور از این گروه از فولادها، كلیه شمش های فولادی است كه پس از تولید و تصفیه فولاد در صنایع فولادسازی به دست میآید. این محصولات به صورت ذیل قابل دسته بندی هستند:
1 شمشه (Bloom) كوره های حرارتی دستگاه نورد محصولات نورد
2 شمشال ( (Billet كوره های حرارتی نورد انواع مفتول نورد لوله های مانسمان لوله های بدون درز
3 تختال ( (Slab كوره های حرارتی نورد تولید ورق
3- ب- محصولات كارشده فولادی
منظور از این گروه از محصولات، كلیه مقاطع پروفیل، لوله، ورق و انواع قطعات فولادی ساخته شده می باشد. تقسیم بندی اینگونه محصولات به شرح ذیل است:
1 مقاطع پروفیل (تیرآهن- نبشی- سپری- قوطی- ریلی- ناودانی- مفتول- میلگرد...)
2لوله (با درز - بدون درز(
3 ورق (ساده - آجدار - گالوانیزه(
4 ریل
4- مواد اولیه لازم برای تولید فولاد
مواد اولیه موردنیاز صنعت فولاد شامل مواد معدنی فلزی و غیرفلزی و گاز می باشد. مواد معدنی فلزی شامل سنگ آهن و سنگ منگنز است. مهمترین ماده معدنی غیرفلزی، ذغال سنگ كُك شو جهت تهیه كك متالورژی است كه به عنوان سوخت و ماده احیاءكننده در تهیه فولاد به روش احیاء غیرمستقیم (كوره بلند) مورد استفاده قرار می گیرد. كمك ذوب ها از قبیل سنگ آهك، كوارتزیت، ماسه سنگ و مواد نسوز (جهت مصرف در كوره های فولادسازی) مانند سنگ ها و خاك های نسوز و دولومیت (جهت تولید آجرهای نسوز) بخش عمده ای از مواد اولیه غیرفلزی را تشكیل می دهند.
یكی دیگر از مواد اولیه موردنیاز تهیه فولاد، گاز طبیعی است كه به عنوان سوخت و ماده احیاءكننده در واحدهای فولادسازی به روش احیاء مستقیم مورد استفاده قرار می گیرد.
آب و انرژی الكتریكی نیز جهت تولید فولاد از ضرورت خاصی برخوردار می باشد كه البته میزان نیاز به آب و انرژی الكتریكی، باتوجه به روش های مختلف فولادسازی متفاوت است. دراینجا اختصاراً به شرح موارد فوق الذكر می پردازیم:
4- الف- سنگ آهن
سنگ آهن یكی از مهمترین مواد اولیه موردنیاز در صنعت فولادسازی است. تقریباً 8/5 درصد از پوسته زمین را آهن تشكیل می دهد و معادن آهن در كشورهای مختلف جهان به طور پراكنده وجود دارند. با برآوردهای انجام شده مجموع ذخایر و منابع آهن در جهان درحدود 215 میلیارد تن می باشد.
شوروی (سابق) با 57 میلیاردتن اولین كشور از نظر ذخایر و منابع سنگ آهن و ایران با بیش از 3 میلیارد تن ذخایر سنگ آهن، پانزدهمین كشور جهان می باشد.
جدول (1) ذخایر سنگ آهن و میزان آهن محتوی آن درایران را مشخص می نماید.
طبق این جدول ذخیره كل سنگ آهن ایران 64/3089 میلیون تن می باشد كه آهن محتوی آن 93/1746 میلیون تن است.
جدول (1) ذخایر سنگ آهن و میزان آهن محتوی آن در ایران (واحد: میلیون تن)
|
4- ب- ذغال سنگ
ذغال سنگ یكی از سوخت های فسیلی است كه در صنعت فولاد اهمیت خاصی دارد. از این ماده در روش كوره بلند به عنوان سوخت وماده احیاءكننده آهن از سنگ آهن استفاده می شود. مقدار ذغال سنگ موجود در جهان بیش از نفت و گاز می باشد و باتوجه به برآوردهای انجام شده ذخایر آن حدود 200 سال آینده دوام خواهد داشت. كل ذخایر تخمینی در حدود 35 تریلیون تن می باشد كه تقریباً 80% آن در سه كشور شوروی(سابق)، امریكا و چین واقع شده است.
در مورد ایران با تأسیس اولین ذوب آهن در اصفهان، عملیات شناسایی و اكتشاف معادن ذغال سنگ در مقیاس صنعتی آغاز شد. عمده ترین معادن آن در نواحی طبس، كرمان و البرز شناسایی شد و استخراج آنها شروع گردید. ذغال سنگ حوزه كرمان در محدوده شهرهای كرمان، طبس و یزد قرار دارد و بزرگترین معدن این منطقه معدن پاب دانا می باشد. ذغال سنگ حوزه البرز، خود به سه منطقه البرز غربی، مركزی و شرقی تقسیم می شود.
مقدار ذخایر ذغال سنگ ایران در سال 1374 حدوداً 3/25 میلیون تن پیش بینی شده است.
4- ج- گاز طبیعی
گاز طبیعی به عنوان ماده احیاء كننده واحدهای احیاء مستقیم در صنعت فولاد اهمیت خاصی دارد. ازنظر ذخایر گاز طبیعی، ایران در بین كشورهای جهان مقام اول را داراست بنابراین در مورد تأمین گاز طبیعی، ماده احیاء كننده واحدهای احیاء مستقیم در كشور مشكلی وجود ندارد.
لازم به ذكر است كه از زمان كشف اولین چاه های نفت در ایران، گاز طبیعی همراه آن سوزانده می شد تا اینكه پروژه انتقال گاز به شوروی(سابق) انجام گرفت و در ازای آن ذوب آهن اصفهان بنا گردید. میزان ذخایر گازهای موجود در میدان های نفتی ایران در جدول(2) آورده شده است.
جدول (2) میزان ذخایر گازهای موجود در میدانهای نفتی ایران (واحد : كیلومتر مكعب)
|
4- د- آب
آب در برخی از مراحل ساخت فولاد ازجمله بخش خنك كننده ها مورد استفاده قرار می گیرد. البته مصرف آب در واحدهای فولادسازی گذشته از اینكه تابع روش تولید و پیشرفت فنون است، تابع شرایط جوی، جغرافیایی و موقعیت واحدها نیز می باشد لذا روش تولید آهن و فولاد، موقعیت جغرافیایی واحدها و نیز توسعه آنها از نقطه نظر میزان مصرف آب در ایران حائز اهمیت است. ایران علی الاصول با كم آبی روبروست و هزینه تأمین آن بالاست، مضاف به اینكه به نظر میرسد حد متوسط مصرف آب واحدهای تولید فولاد ایران به دلیل شرایط جوی و بالابودن درجه حرارت در اغلب نقاط ایران نسبت به اروپا، درصورت یكسان بودن روش تولید، بالاتر است.
4- ه- انرژی الكتریكی
فرآیند فولادسازی در مراحل مختلف، نیاز فراوانی به انرژی الكتریكی دارد. به عنوان مثال این نیاز برای شركت فولاد مباركه حدود 600 مگاوات می باشد.
به همین جهت محل استقرار واحد فولادسازی بایستی با درنظر گرفتن شبكه برقی سراسری كشور صورت پذیرد.
به طور كلی میزان تولید و مصرف انرژی الكتریكی در كشورها از عوامل عمده برای ارزیابی درجه صنعتی بودن آنها به شمار می آید و هزینه انرژی الكتریكی نیز تابع نحوه تولید آن است و همچنین همان طوری كه گفته شد باتوجه به نیاز واحدهای فولادسازی به این انرژی، اهمیت این موضوع در بررسی اقتصادی تولید آهن و فولاد واضح است.
5- مراحل تولید
همان طور كه ذكر آن گذشت، محصولات فولادی به شكل های مختلف مانند: ورق، تسمه، میلگرد، پروفیل، تیرآهن و... تهیه می شوند. عملیات تهیه فولاد به طور خلاصه شامل مراحل ذیل است:
مواد خام (سنگ آهن( آهن خام فولاد ریخته گری شمش نورد اولیه عملیات كار مكانیكی محصولات نهایی.
6- روش های عمده تولید آهن خام
6- الف- تهیه آهن خام از روش كوره بلند
تهیه آهن از این روش دارای سابقه طولانی است. اولین كوره بلند درسال 1600 میلادی در انگلستان ساخته شد و استفاده تجاری از آن با روش پیش گرم نمودن هوای ورودی از سال 1800 میلادی آغاز گردید. در این روش سنگ آهن پس از استخراج از معدن، به اندازه مشخص دانه بندی می شود.
سپس سنگ آهن خرد شده به همراه مقداری پودر كُك به واحد كلوخه سازی صورت به و كك پخته آهك همراه به شده شود و نهایتا بار آماده ی ارسال لایه های متناوب سنگ آهن، كك و آهك به داخل كوره شارژ می گردد. از قسمت پایین كوره هوای پیش گرم شده به همراه گاز طبیعی و یا حتی به همراه مقداری گاز اكسیژن دمیده می شود. سوختن كك در منطقه دمنده ها باعث تولید گاز Co و حركت روبه بالای گاز احیاء كننده می گردد. درنهایت سقوط تدریجی مواد از بالا به پایین كوره و حركت روبه بالای گاز احیاءكننده باعث احیاء و ذوب تدریجی اكسیدهای آهن می گردد. واكنش های كلی اكسیدهای آهن به فرم ذیل است :
Fe2o3 + 3Co 2Fe + 3Co2
آهن خام حاصل از كوره بلند حاوی 3 تا 5 درصد كربن و 2/0 تا 1 درصد فسفر و حدود 1 درصد گوگرد است كه به واحدهای فولادسازی منتقل می شود. بعد از فرآیند كوره بلند، عملاً فولادسازی در كنورتورها صورت می گیرد كه در قسمت های بعدی به آن اشاره می شود.
6- ب- تهیه آهن از روش احیاء مستقیم
احیاء مستقیم كانه های آهن به روش هایی اطلاق می شود كه اكسیژن كانه در دمایی پایینتر از دمای ذوب یا نرم شدن كانه به وسیله كربن، حذف شود و تغییر شكلی درصورت ظاهری كانه آهن یا گندله در طی احیاء به وجود نیاید. به علت ثابت ماندن شكل ظاهری نمونه، آهن تولید شده به صورت اسفنج مانند درآمده و به این علت به آن آهن اسفنجی گفته می شود.
بیش از 50 روش صنعتی، نیمه صنعتی و آزمایشگاهی احیاء مستقیم در سطح دنیا توسعه یافته است. در ایران به دلیل وجود ذخائر منابع گاز طبیعی ،روش احیاء مستقیم روش مناسب و اقتصادی می باشد.
«شمای كلی فرآیندهای تولید دركوره بلند»
7- فرآیندهای فولادسازی
باتوجه به اینكه آهن خام دارای 3 الی 4 درصد كربن می باشد، بایستی كربن اضافی آن به نحوی حذف شود. در عملیات فولادسازی 3 روش عمده مورد استفاده قرار میگیرد كه عبارتند از:
1 روش كنورتوری 2 روش كوره ای زیمنسمارتین 3 كوره های قوس الكتریكی
8- ریخته گری
بعد از تنظیم تركیب و دمای فولاد، عمل تخلیه مذاب فولاد به داخل پاتیل (Ladle) صورت می گیرد.(در بعضی موارد، در این مرحله عناصر آلیاژی در پاتیل اضافه می شود)، سپس عملیات شمش ریزی صورت می گیرد. به طور كلی شمش ریزی به دو روش عمده پیوسته و غیرپیوسته صورت می گیرد.
در روش غیرپیوسته، مذاب به داخل قالب های چدنی به صورت های مختلف مقطع دایره، مربع و یا چندگوش ریخته می شوند و نهایتاً بر روی این شمش ها عملیات كار مكانیكی صورت می گیرد.
در ریخته گری پیوسته، مذاب به طور مداوم در قالب های مس ریخته می شود. سرعت تولید، كیفیت شمش ازلحاظ ناخالصی ها و ساختار شمش های تولیدی در این روش به مراتب مناسب تر از روش غیرپیوسته است.
-9عملیات مكانیكی اولیه )نورد یا آهنگری اولیه(
اغلب شمش ها دوباره تا دمای بالا گرم می شوند، به مدت زمان مناسب نگهداری شده و سپس نورد یا آهنگری می شوند تا به شكل موردنظر برسند.
در ریخته گری پیوسته، مستقیماً به محصولات نیمه نهایی می رسیم، محصولات نیمه نهایی موردنظر شامل مقاطع تختال (Slab) ، شمشه (Bloom) و شمشال (Billet) است.
مطابق شكل:
|
|
|
( Billet) (Bloom ) (Slab )
محصولات نیمه نهایی با انجام عملیات كار مكانیكی گرم یا سرد (نورد، آهنگری، اكستروژن و كشش عمیق) به محصولات نهایی مانند ورق، میلگرد و اشكال پروفیل ساختمانی تبدیل می شوند.
برای حصول استحكام و شرایط ویژه مقطع موردنظر، عملیات حرارتی انجام می شود تا ساختار و خواص فولاد را بتوان تغییر داد یا كنترل نمود.
10- سیر تكاملی تولید فولاد
استخراج فلز آهن از سنگ آهن با یك عمل شیمیایی صورت می گیرد. به این معنی كه سنگ های اكسیدی آهن به وسیله كربن احیاء و عنصر آهن آزاد می شود كه این فرآیند را می توان به صورت خلاصه شده ذیل مشاهده نمود:
2C + O2 2CO
C + O2 CO2
Fe2O3 + 3Co 2Fe + 3Co2
Fe3O4 + 4Co 3Fe + 4Co2
قرن ها ذغال چوب (كربن) به عنوان عامل احیاءكننده به كار می رفت ولی ازسال 1907 كك جای آن را گرفت كه به عنوان مهمترین سوخت كوره بل ند نیز بكار می رود. از این تاریخ كوره ها ارتفاع بیشتر پیدا كرد و حجیم تر شد ولی فعل و انفعالات داخلی آن تقریباً بدون تغییر بوده است. انسان اولیه معلوم نیست چگونه و از كجا سنگ آهن را كشف و ذوب نمود و فلز آهن را به دست آورد. اما از شواهد امر پیداست كه از 2400 سال پیش و شاید هم بیشتر، انسان اولیه آهن را شناخته است. به نظر می رسد ابتدا شهاب سنگ های آسمانی مورد استفاده انسان های اولیه قرار گرفته باشد. اطلاق سنگ و فلز آسمانی به آهن توسط انسان های اولیه مؤید همین امر است. انسان های اولیه بر وجود فلز خالص آهن در همین شهاب ها آگاهی یافته و آنرا مورد استفاده قرار داده اند. ولی مقدار آن البته كم و به علاوه در نقاط مختلف كره زمین پراكنده بوده است بعدها انسان اولیه سنگ آهن را شناخت چه بسا ممكن است كه سنگ آهن مجاور آتش سوزی جنگلی بوده و جریان شدید باد، این آتش سوزی را تشدید و ذغال چوب حاصله از سوختن درختان جنگل، سنگ آهن را احیاء كرده و آهن مذاب در خاكستر های ذغال چوب به دست بشر اولیه رسیده و یا سنگ های آهن به كوره های كوزه گری كه قدمت بیشتری دارد راه پیدا كرده و در این كوره ها بر اثر حرارت زیاد حاصل از سوختن ذغال چوب احیاء شده و فلز آهن به دست آمده باشد.
بعدها ذوب آهن در كوره های ابتدایی كه با سنگ یا آجر ساخته میشد، انجام گرفت.
جریان كار این كوره ها تا قبل از اختراع دم تابع اتفاقات طبیعی و جریان هوا بوده است و به این جهت بشر دوران های اولیه ناچار بوده است كوره های خود را در میان دره ها بسازد و از جریان طبیعی باد داخل دره استفاده كند ولی پس از پیدایش دم، بشر توانست هركجا بخواهد كوره را بسازد و با استفاده از دم، كار ذوب را منظم تر انجام دهد.
سوخت این كوره ها ذغال چوب (تقریباً كربن خالص) بوده است و هنوز هم باوجود پیدایش ذغال سنگ، در ممالك اسكاندیناوی به علت نبودن ذغال سنگ و وسعت جنگل های آن در كوره های ذوب آهن، ذغال چوب مصرف میشود. كاربرد ذغال چوب به عنوان سوخت كوره بلند قرن ها ادامه داشت. ذغال چوب به علت فرآیند تهیه خاص آن، هزینه بالایی داشت.
همچنین هوای لازم در كوره ها به سختی راه خود را می یافته و به همین جهت ساختن كوره های خیلی بلند مقدور نبوده و ارتفاع كوره های این زمان از 10 متر تجاوز نمی كرده است، زیرا ارتفاعی بیشتر از آن حد باعث مسدود شدن كوره می شده است. كوره بانان در این زمان ناچار بودند كوره ها را پس از هر نوبت كار تعطیل نموده و پس از نظافت، لكه گیری و تعمیرات، آن را به كار بیندازند.
با به كار بردن ذغال چوب، برای بدست آوردن هرتن آهن در حدود 6 تن ذغال چوب لازم بوده است. بارگیری كوره با سنگ های درشت دست چین آهن انجام می گرفته و در نتیجه بهترین محصول آهنی در نقاطی به دست می آمده كه سنگ آهن غنی تری داشته است مثل سوئد، اتریش.
Darby، برای اولین مرتبه سوخت كك را بكار برد. مزایای كك عبارتند از تخلخل، سختی، فراوانی و ارزانی آن كه این مزایا باعث شدند بتوان ارتفاع كوره را زیاد كرده و این موضوع مشكل مسدود شدن كوره ها را مرتفع نمود. استفاده از كك به جای ذغال، به دلایل دیگر، یكی از عمده ترین قدم ها در سیر تكاملی تولید آهن و فولاد به شمار می رود، ازجمله اینكه درطول قرن هیجدهم ، با گسترش ظرفیت كوره های تولید آهن ، خطر نابودی جنگل ها احساس می شد كه در رابطه با این موضوع پس از تقطیر ذغال سنگ و تولید كك، حركت بسیار نوینی صورت گرفت.
تحول دم ها از دستی و پایی به آبی كه فشار آب چرخی را می چرخانده و حركت چرخ نیز دم را باز و بسته می كرده است، تا اختراع ماشین بخار ادامه داشت و چند سال بعد از اختراع ماشین بخار، دم های ماشینی متداول شد كه به مراتب از دم های اولیه قوی تر بود. به این ترتیب ارتفاع كوره ها از 10 متر به 30 متر و قطر شكم كوره نیز از 60 سانتیمتر به حدود 8 متر رسید. درسال های بعد نیز پیشرفت هایی ازجمله موارد ذیل اتفاق افتاده است:
1 كاربرد سنگ آهك به عنوان ماده گداز آور كه با ناخالصی های همراه با سنگ آهن تركیب و سرباره سیالی را تشكیل میدهد كه میتواند مستقل از آهن مذاب جریان پیدا كند
2 كاربرد سیستم خنك كننده دیواره های كوره با آب كه باعث دوام بیشتر آجرهای نسوز پوششی كوره می شد و عمر كوره را تا حد چند سال بالا می برد.
3 گرم كردن هوای دم كوره كه باعث صرفه جویی قابل ملاحظه ای در مصرف سوخت بود.
4 تعبیه دستگاه های دو قیفی در دهانه كوره جهت بارگیری كوره ها كه خروج غیر آزاد گازهای كوره را امكان پذیر می كرد.
5 ساختن كارخانه های فولادسازی در جوار كوره های بلند كه جمعاً یك واحد صنعتی را تشكیل می داد.
لازم به ذكر است كه كوره های ذوب آهن از آن زمان كه با دم های دستی كار میكرده تا زمان حاضر راهی بس طولانی پیموده ولی اصول فعل و انفعالات شیمیایی داخلی آن یعنی بالابردن دمای كوره به وسیله احتراق كربن به كمك هوای دم و احیای اكسید آهن به وسیله كربن، همان است كه از اول بوده و تاكنون تغییری نكرده است.
11- تاریخ فلزات و ذوب فلزات تا قرن نوزدهم
انسان سودمندی فلز را در سرزمینی میتواند كشف كند كه فلزات و سنگ های معدنی در آن سرزمین وجود داشته باشد و ایران چنین سرزمینی است. شواهد دیرین شناسی نشان می دهد كه شمال و مركز ایران قدیمی ترین نقطه متالورژی در دنیای قدیم بوده است و ساكنان فلات ایران جزو اولین اقوامی بوده اند كه به كشف فلز دست یافته اند.
ایران سرزمین غنی از سنگ های معدنی است. سلسله جبال البرز غنی از همه سنگ های معدنی و مواد سوختی است و متالورژی از این نقطه به آسیا، آفریقا و اروپا انتشار یافته است. حفاری های براون در شمال ایران، گیرشمان در تپه كیان در مغرب و اِشمیت در تپه حصار شمال و هرتسفلد در تل باگون در جنوب ایران به این نتیجه منجر شد كه در اواخر نئولیتیك (نوسنگی) پس از یك دوران سرسبزی به تدریج یك دوره خشكی در دره ها ایجاد گردید و مردم به زندگی در دشت ها گرایش یافتند. ایران به علت غنای مواد معدنی خود، همیشه مورد تجاوز و توجه كسانی بوده كه خود را به قدر كافی قدرتمند احساس می كرده اند. این كشور، در حالی كه راه عبوری برای سرب ارمنستان بود، خود نیز ثروتی از طلا، مس و قلع داشت. در جریان نیمه دوم هزاره سوم قبل از میلاد، كاربرد فلز افزایش یافت. كشفیات شوش، تپه حیدر، تپه كیان، تپه گئوی حاوی شمار زیادی ابزار آلات مفرغی و نقره ای است. اما در ایران، عصر مفرغ، در سال 2000 قبل از میلاد كاملا استقرار یافته بود بیشتر اشیاء مفرغی این دوره ظاهراً در قالب سنگی ریخته گری شده و قالب ها با مجاری تغذیه فلز مذاب و هواكش مجهز بوده اند. اولین آثار آهن در همین زمان ظاهر شده گرچه فقط برای زیورآلات به كار میرفته است محتوای زیاد نیكل آن (حدود 5 درصد) نشان می دهد كه باید از سنگ های شهابی به دست آمده باشد. اسامی كه اقوام مختلف در این زمان برای آهن بكار می برده اند عبارت بودند از: پارزیلو توسط آشوری ها و بابلی ها، بارزا توسط سومری ها، بارزل توسط عبری ها و با انپت توسط مصری ها. ترجمه این اسامی (فلزی از آسمان: Metal from Heave) نشان می دهد آهنی كه در این زمان به كار رفته منشأ آسمانی داشته، یعنی از سنگ های ثاقب به دست آمده است.
12- ذوب آهن از قرن نوزدهم تا زمان حاضر
فكر ایجاد صنایع جدید و كوشش های اولیه برای معرفی صنایع ماشینی در ایران در زمان فتحعلی شاه قاجار، ابتدا از سوی عباس میرزا، آغاز شد. در آن زمان به كمك كارشناسان فرانسوی، كارخانه های تفنگ سازی و توپ ریزی در اصفهان و تبریز، احداث شده بود. در اولین روزنامه ای كه به مدیریت میرزا صالح شیرازی در رمضان 1252 هجری منتشر شد این جمله نوشته شده بود «جعفرقلی بیك افشار ازطرف عباس میرزا برای شناختن فن آهن ریزی به او مدتی در معادن سیبری كار كرد و پس از بازگشت به روسیه فرستاده شد» ایران در معادن نائیج مازندران به گلوله ریزی پرداخت و در یك سال صدهزار گلوله ریخت و به توپخانه فرستاد. در زمان فتحعلی شاه فرانسوی ها برای تجهیز واحدهای آهن ریزی در ایران همكاری هایی داشته اند در آن زمان با همكاری ژنرال گاردان كارخانه های توپ ریزی در اصفهان، قزوین، مشهد، شیراز و بندرعباس دایر شد و گلوله ریزی مازندران مجدداً شروع بكار كرد:
در نخستین سال های سلطنت ناصرالدین شاه (1227 تا 1275 شمسی) از سوی میرزاتقی خان امیركبیر و همفكرانش اقدامات لازم جهت احداث صنایع زیربنایی با جدیت بیشتری دنبال شد اما با بركناری امیركبیر صنایع نوپایی كه به همت او وپیروانش برپا شده بود ازمیان رفت و توسعه صنعتی كشور كه آغاز شده بود عقیم ماند.
12- الف- كوره تولید آهن
حدود سال 1266 شمسی حاج محمدحسن امین الضرب اجازه و انحصار تأسیس كارخانه تولید آهن را برای استقرار در شهر نور، به مدت سی سال از ناصرالدّین شاه گرفت. او به این منظور، توربین های بخار، كوره های دمشی و نیز سایر تجهیزات یك واحد فولادسازی را از فرانسه خرید. ارتفاع كوره خریداری شده توسط امین الضرب ،8 متر و تولید آن 15 تن آهن خام در شبانه روز بوده است این تجهیزات قرار بود ازطریق محمودآباد به محل استقرار واحد در شهر نور انتقال یابد. در اطراف آن محل هم معادن آهن و هم ذغال سنگ وجود داشته است. معادن ذغال سنگ ماهان نیز در همان جا قرار دارد. چون حمل تجهیزات این واحد از محمودآباد به نور، ممكن نبوده، امین الضرب با پرداخت خسارت از اجرای این طراح منصرف شد سپس تصمیم گرفت كارخانه تولید آهن كوچكتری احداث كند كه آن هم با شكست روبه رو شد.
12- ب- آهن ریزی در ایران
در زمان امیركبیر عده ای برای فراگرفتن فنون به خارج اعزام شدند ازجمله صادق كربلایی به روسیه فرستاده شد. او در كارخانه های آهن ریزی مسكو این فن را آموخت و پس از مراجعت به كارخانه داوودیه و سپس در قورخانه عهده دار ریخته گری شد آهن ریزی داوودیه در زمان ناصرالدین شاه در سال 1264 شمسی در شمال تهران تأسیس گردید. برای این واحد كانه آهن از پس قلعه و ذغال سنگ از معادن شمشك تأمین می شد. برخی معتقدند كه در این واحد كوره بزرگ كوپل و ریخته گری وجود داشته و فقط آهن قراضه آب می شده است. این واحد توسط ناصرالدین شاه افتتاح و اولین كارخانه آهن ریزی ایران بود. تولید در این واحد بیش از چندین ماه به طول نینجامید و از این واحد اطلاعات بیشتری در دسترس نیست.
دومین واحد آهن ریزی ایران در زمان ناصرالدین شاه در قورخانه تهران تأسیس شد.
در این واحد آهن توسط كوره های زمینی ذوب می شد. در قورخانه درسال 1268 شمسی مجسمه ناصرالدین شاه توسط استاد صادق كربلایی ریخته شد كه در باغ شاه نصب شد. سومین كارخانه آهن ریزی در ایران درسال 1269 شمسی در كارخانجات راه آهن حضرت عبدالعظیم توسط یك كمپانی بلژیكی تأسیس شد در آن واحد توسط كورهای بزرگ، ذوب و ریخته گری چدن انجام می گرفت. درسال 1283 شمسی كارخانجات مختلفی ازجمله توسط شركت ایران و انگلیس در ایران دایر شد كه با كوره های بزرگ و به كمك كك كار می كرد. در آن زمان تأسیسات ریخته گری در بندر انزلی تأسیس شد.
در زمان مظفرالدین شاه، صنیع الدوله كوره آهن ذوب كنی به كشور وارد كرد كه در داودیه شمال تهران نصب شد او درنظر داشت سنگ آهن آن را از كوه های پس قلعه و ذغال سنگ آن را از معدن شمشك تأمین كند ولی، پس از چند ماه به علت بروز اشكالاتی در زمینه بهره برداری، كار آن متوقف ماند. پس از كودتای 1299 شمسی قورخانه توسط مهندسان آلمانی توسعه یافت. در سال 1306 شمسی در این واحد ریخته گری فلزات آلیاژهای آهنی و غیرآهنی تأسیس شد در این واحد كوره بزرگی به ظرفیت دوتن چدن مذاب در هر ساعت وجود داشت كه با كك كار می كرد. مضافاً اینكه چندین كوره بوته ای به ظرفیت های بین 100 تا 150 تن وجود داشته كه ظرفیت كل تولید آنها حدود یك تن چدن مذاب بود در این واحد ازجمله ابزار تفنگ و فشنگ و سایر مهمات ساخته می شد
در سال 1344 قراردادی بین سازمان برنامه و نمایندگان كنسرسیوم دماك- گروپ آلمان برای احداث یك كارخانه ذوب آهن با كوره قوس الكتریكی به امضاء رسید. محل احداث این كارخانه در منطقه چمزمان شمس آباد درنظر گرفته شد. به دنبال امضای این قرارداد و اظهارنظر كارشناسان امریكایی و تأیید كارشناسان ایرانی كه ظرفیت پیشنهادی را اقتصادی نمی دانستند و ایجاد واحدهای بزرگتر نیز، به دلیل كافی نبودن مواد اولیه داخلی مورد موافقت بانك جهانی قرار نگرفته بود، این قرارداد، لغو شد.
در تیرماه 1339 كارشناسان ایرانی و بانك جهانی نتیجه گیری كردند كه قبل از حصول اطمینان از وجود و كفایت مواد اولیه، احداث مجتمع فولادسازی در كشور صحیح نیست و پیشنهاد كردند كه ابتدا كارخانه نورد به ظرفیت 300 هزارتن و قابل توسعه تا 500 هزار تن در كرج احداث شود و در مرحله بعد كارخانه فولادسازی تأسیس گردد. ایجاد كارخانه ذوب آهن در صدر تلاش های دولت برای صنعتی كردن كشور قرار داشت ولی قراردادهای مختلف منعقده به دلیل نبودن یك سازمان مسؤول هدایت و پیگیری و نداشتن یك سیاست صنعتی و اقتصادی به شكست انجامید.
در آذرماه 1338 قانون تأسیس سازمان ذوب آهن به تصویب مجلس شورای ملی رسید و در 23 دیماه 1338 سازمان ذوب آهن ایران به منظور تأسیس كارخانه تولید آهن و فولاد تشكیل شد. این تصمیم اقدام عملی درجهت پركردن خلأ یك سازمان مستقل و متولی این امر بود و عملیات شناسایی و اكتشاف مواد اولیه شروع شد.
سپس مذاكراتی بین دولت ایران و اتحاد جماهیر شوروی سابق صورت گرفت و در فضای خاص سیاسی آن روز منجر به امضاء موافقت نامه ای برای تأسیس یك كارخانه ذوب آهن و یك كارخانه ماشین سازی در ایران و احداث خط لوله سراسری گاز و صدور گاز طبیعی به شوروی شد.
پس از انجام مطالعات اولیه در عملیات زمین شناسی، توپو گرافی، مقدمات ساختمان كارخانه در نیمه دوم سال 1346 فراهم شد ودر 23 دیماه 1350 كوره بلند ذوب آهن اصفهان، به بهره برداری رسید.
به موازات فعالیت های دولت در زمینه استقرار و ایجاد و صنعت فولاد، بخش خصوصی احداث كارخانه نورد را كه مستلزم سرمایه گذاری كمتر، دوران ساخت كوتاه تر، تكنولوژی ساده تر و منافع بیشتری بود، موردتوجه قرار داد. به این ترتیب، پروانه تأسیس كارخانه نورد برای بخش خصوصی در سال 1342 صادر شد و در سال 1346 اولین كارخانه نورد مفتول به ظرفیت 65000 تن در سال و در 10 كیلومتری شهر اهواز به بهره برداری رسید.
تولیدات این كارخانه مفتول ساده وآجدار بود كه ازطریق نورد شمش وارداتی تولید می شد. افزایش روزافزون تقاضای فولاد كشور و سود قابل توجهی كه عاید بخش خصوصی می شد، موجب شد كارخانه های نورد جدیدی در كنار كارخانه اول احداث و به این ترتیب مجموعه ای از كارخانه های نورد جهت تولید فولادهای ساختمانی، لوله سازی، پروفیل سازی، توری سازی و سایر صنایع فلزی تا سال 1351 تأسیس و به تدریج به بهره برداری برسد. در سال 1348 بخش خصوصی برای تهیه شمش موردنیاز كارخانه های نورد، اقدام به تأسیس كارگاه های ذوب الكتریكی به نام ذوب شوش وشهریار كرد، كه با استفاده از كوره های قوس الكتریكی و ذوب آهن قراضه، شمش موردنیاز كارگاه های نورد را تهیه كند. بهره برداری از این واحدها با ظرفیت اسمی سالیانه 360 هزارتن، ازسال 1351 آغاز شد. بخش خصوصی به دلیل قانون مالكیت دولتی صنایع مادر و در حقیقت به علت مشكلات تهیه و آماده سازی آهن قراضه، اداره این كارخانه ها را در سال 1355 به دولت واگذار كرد. این واحدها تا سال 1365 تحت پوشش مجتمع فولاد اهواز اداره می شد و در این سال به صورت شركت مستقل تابع شركت ملی فولاد ایران و از سال 1368 تحت پوشش گروه ملی صنعتی فولاد ایران قرار گرفت.
در تاریخ 17 خرداد 1353 موافقت نامه ای بین ایران و ایتالیا در رم به امضاء رسید و توافق شد چند پروژه بزرگ به شركت های ایتالیایی واگذار شود ازجمله پروژه تولید فولاد در بندرعباس. در سال 1356 به دلیل دوربودن محل مجتمع از منابع داخلی آهن قراضه و به صرفه نبودن واردات آهن قراضه، جهت خودكفا كردن مجتمع از منابع داخلی، پروژه از بندرعباس به مباركه اصفهان انتقال یافت و درسال 1372 شركت مجتمع فولاد مباركه به بهره برداری رسید.